As dual-chamber air springs become more common, many have noticed that the aluminum upper seat has been replaced with plastic components. Is this change merely a cost-cutting measure driven by competition? Certainly not! Understanding the dual-chamber air spring reveals that its main and auxiliary air chambers are actually formed by internal partitions, reinforcing ribs, and tortuous air passages within the upper seat. Therefore, the structure of the dual-chamber air spring upper seat is quite complex, requiring high dimensional precision, making it difficult to manufacture using traditional metal materials. High-performance polymer composites combined with special welding processes have become the mainstream solution for producing dual-chamber air spring upper seats. The manufacturing and welding quality of the upper seat is illustrated in the provided images, showing that the upper seat is formed by welding two plastic components, which include complex air passages, various shaped reinforcing ribs, and an installation seat for the solenoid valve. As the air chamber, the upper seat must withstand internal air pressures of around 25 bar, placing high demands on the quality of the plastic welding. So how do we assess the quality and reliability of plastic welding? The answer is straightforward: through burst testing, where the welded upper seat is subjected to explosive pressure. But is it just about the burst pressure level? NO! Here are some key insights: 1. The burst pressure must meet certain requirements but higher is not always better; 2. The form of the explosion rupture is more important than the burst pressure value itself. To elaborate: 1. Burst Pressure: It must be sufficient, but not excessively high. The air spring needs to withstand high internal pressure, and the upper seat must meet a certain burst pressure value to ensure basic strength. However, during operation, the upper seat material is subjected not only to internal pressure loads but also to complex alternating stresses caused by the vehicle's body and unsprung mass, which are multi-directional. The burst pressure only reflects the strength of the upper seat under localized internal pressure; too high a burst pressure can result in excessive rigidity, leading to stress concentration under loads from other directions. Additionally, the injection molding and welding processes can create significant residual internal stresses that cannot be released, negatively affecting durability. 2. Explosion Rupture Form: More critical than pressure value. After conducting numerous burst tests and durability trials, the team has categorized the rupture forms into three types based on their positions, summarizing their impacts accordingly. Key methods to enhance the quality of plastic welding include: 1. Improving the uniformity of the welding surface temperature. The melting temperature of nylon is close to its thermal decomposition temperature; if temperature uniformity is poor, it can cause local overheating (thermal decomposition) or areas that are not fully melted, leading to welding defects. 2. Controlling the moisture content of the plastic components. Nylon has a strong water absorption capacity, and excessive moisture content can create bubbles and other defects during welding, affecting welding strength. 3. Ensuring appropriate clamping force. The correct approach is to ensure good contact between the plastic parts while avoiding excessive extrusion of the melted material, allowing the welded joint to form a robust connection (as shown in the left image below). A well-formed joint can enhance strength and longevity. In contrast, an incorrect case involves excessive extrusion of melted material, leaving minimal connecting material between the two sides of the plastic body, which can lead to rapid fatigue and fracture under alternating stresses (as depicted in the middle and right images below). Konghui Technology has delivered 700,000 related products. The welding process for PA6GF50 and other high-performance polymers is complex, and the necessary equipment technology was previously unavailable domestically. Suzhou Kaierbo and other local equipment manufacturers have overcome the technology for hot air welding machines, providing equipment support for the plastic welding of dual-chamber air spring upper seats. Through ongoing research and process optimization, by June 31, 2025, Konghui Technology has cumulatively welded and delivered 700,000 plastic upper seats for dual-chamber air springs, achieving zero feedback on welding quality issues in after-sales, showcasing the domestic technical strength in this field. With the development of intelligent suspension technology, plastic welding processes will play an increasingly critical role in the air spring sector, providing solid support for vehicle comfort and safety.
The Shift from Aluminum to Plastic in Dual-Chamber Air Springs: A Technological Advancement
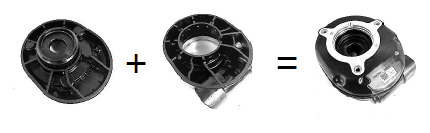
Images
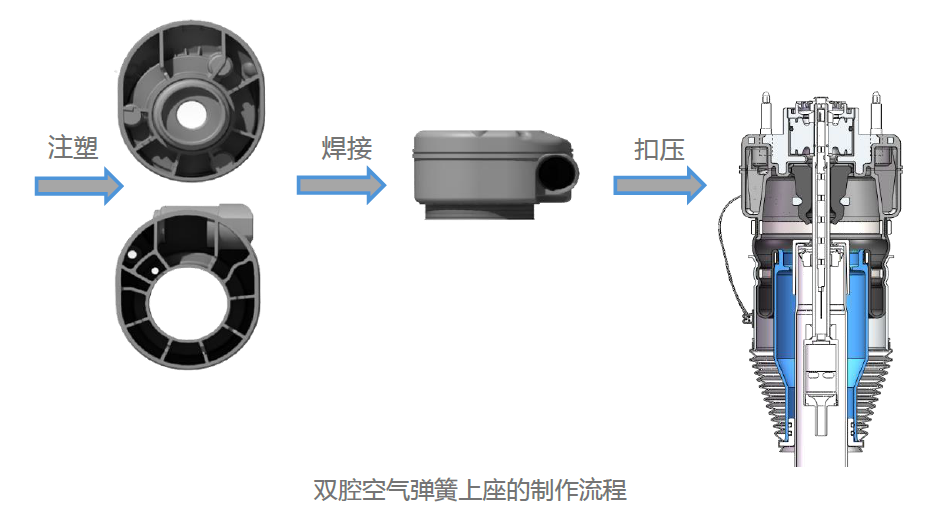
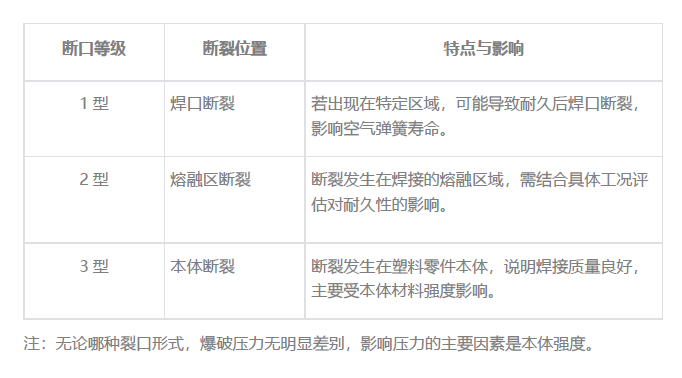
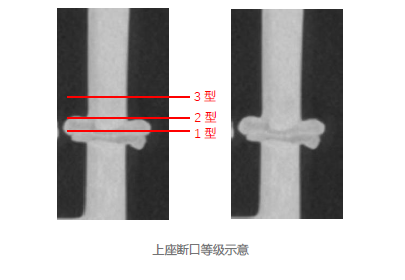
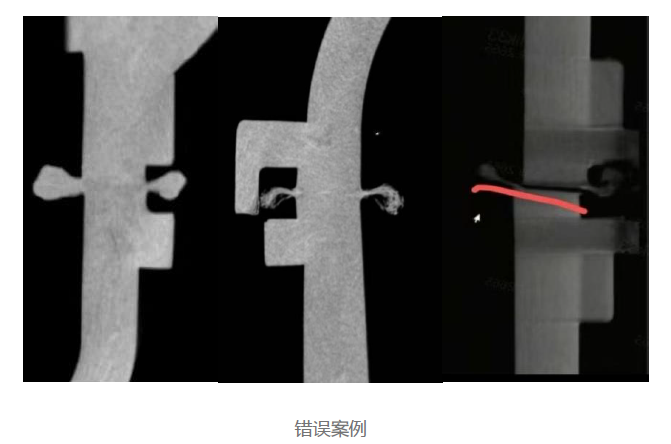
Share this post on: