The seamless cooperation between soft and hard tissues is essential for the powerful sprint of a leopard, the graceful glide of a snake, and the dexterous grip of humans. Muscles, tendons, ligaments, and bones work together to provide energy, precision, and range of motion, enabling complex movements commonly seen in the animal kingdom. Replicating this diversity of musculoskeletal systems in robotics poses significant challenges. So far, using multi-material 3D printing has been a method to create soft and hard robots. Although this approach can simulate the diversity of biological tissues, it means key properties in the robotic structure, such as stiffness or load-bearing strength, cannot be consistently controlled. According to foreign media, a team at the École Polytechnique Fédérale de Lausanne (EPFL), led by Josie Hughes from the CREATE lab focused on computational robot design and manufacturing, has developed an innovative lattice structure that combines the diversity of biological tissues with robotic control and precision. The lattice is made from simple foam materials and consists of multiple independent units (cells) that can be programmed to adjust to different shapes and positions. These cells can exhibit over one million different configurations and can even combine into infinite geometric variations. 'We utilized programmable lattice technology to construct a bio-inspired elephant robot that features a soft trunk capable of twisting, bending, and rotating, alongside more robust hip, knee, and foot joints,' said postdoctoral researcher Qinghua Guan. 'This indicates that our approach provides a scalable solution for designing unprecedentedly lightweight and adaptable robots.'
EPFL Develops Innovative Lattice Structure for Bio-Inspired Robots
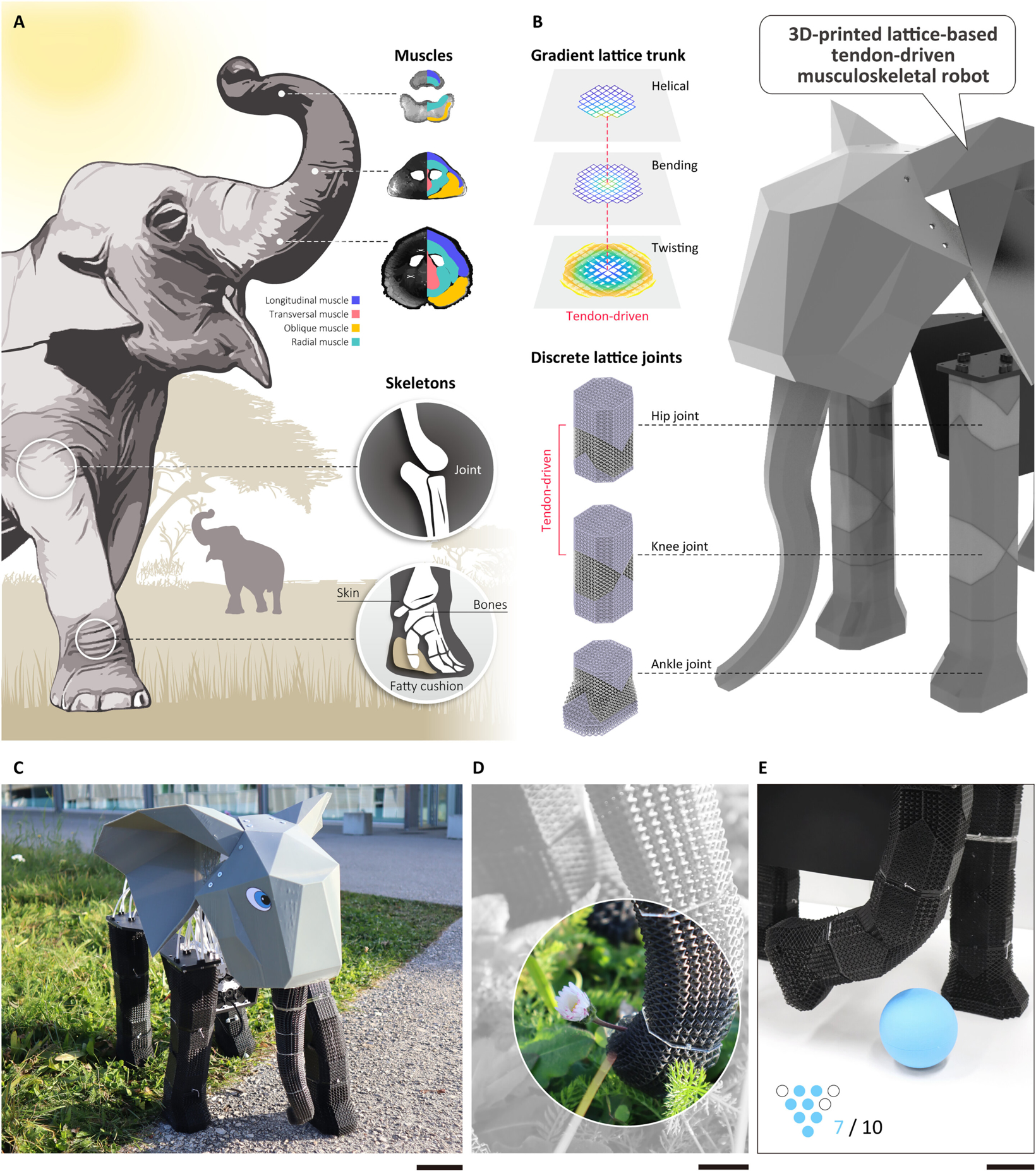
Share this post on: